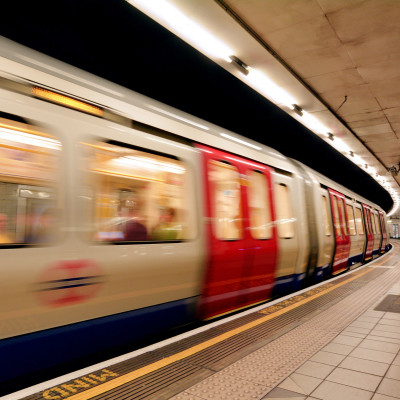
IndySoft goes UNDERGROUND
A Case Study on how London Underground Limited was able to reduce costs and increase in-house calibrations with the implementation of IndySoft.
BACKGROUND
With a history that dates back to 1863 when it was the world’s first underground railway, what is now known as the London Underground has continuously evolved to meet the expanding transport needs of Greater London and parts of the counties of Buckinghamshire, Hertfordshire and Essex. Operated by London Underground Limited (LUL), the Underground is an immense network that serves 275 stations and encompasses over 408 km of railway, ensuring that an astonishing three million passenger journeys are made daily.
To help ensure the safety and efficient operation of the tube, LUL engineers have access to more than 20,000 instruments and gages. In addition to specialized and bespoke equipment, the extensive inventory includes track gages, multi-meters, torque wrenches, crimp tools, verniers, micrometers, and electrical and pressure gages.
To certify the continued accuracy of LUL’s gages and instruments, calibration procedures are performed by a team of skilled calibration engineers at LUL’s Lillie Road depot in Fulham. Each calibration staff member has access to a variety of highly accurate, UKAS traceable calibration apparatus, including torque testers, digital height gages, manometers, plus electrical and pressure test equipment.
CHALLENGES
It is the calibration department’s job to track the location of these gages and instruments and to ensure that each piece of equipment remains in calibration. In addition to LUL’s huge gage and instrument inventory being distributed over multiple locations that have several different departments, items can also be booked-out and used on-site. Given that LUL’s calibration procedures takes place either on a 6 month or 12 month cycle, the status and tracking of 20,000 instruments and gages has previously presented extremely challenging logistical problems.
LUL’s calibration facility previously operated a business process compliance system, although, as LUL’s gage and instrument inventory grew, this inflexible software struggled to handle the large volumes of records and the required management tasks.
To help overcome these difficulties a search was made to find a flexible software package that was able to match all of the company’s stringent demands, and that would also remain ‘future-proof’ as LUL’s gage and instrument inventory grew.
INDYSOFT HAS THE ANSWER
Having considered several other options, IndySoft was judged to be the most suitable software for both current and future needs.
During onboarding all existing gage data and history was imported directly into the IndySoft program from LUL’s older application, without any problems. Following a short training period, staff were immediately able to make use of all basic tasks. Then, as IndySoft proved to be intuitive and easy to use, more advanced functions were quickly mastered.
As LUL’s calibration department has quite specific requirements, the help and support provided by IndySoft allowed the software to be configured to suit the department’s own particular needs. Now, as IndySoft introduces additional software features, LUL staff makes use of the company’s readily available support. For instance, with IndySoft’s assistance, LUL recently implemented an IndySoft feature that, at the start of every month, allows the department to automatically email its ‘customers’ with a calibration-due reminder.
Due to the many ‘equipment status’ options available in the software, such as ‘in-use’, ‘external calibration’, ‘archived’, ‘lost’, ‘stolen’ and ‘scrapped’, LUL can now accurately record the exact status of every piece of its equipment.
Through the trouble-free communication between many instruments’ commonly used software, the use of IndySoft has allowed LUL to bring previously externally calibrated instruments, such as multimeters and clamp meters, in-house. This means that, in addition to achieving considerable cost savings, increased in-house work has drastically reduced calibration turnaround times. So successful has the adoption of IndySoft been, LUL recently added additional licenses.
CAN INDYSOFT HELP YOU?
London Underground’s experience with IndySoft Calibration and Asset Management Software illustrates the system’s unmatched ability to manage complicated gage inventories, across multiple sites. The use of the flexible software is equally applicable to the management of the gage stocks of smaller concerns as well. Contact us at sales@indysoft.com to have a discussion about your organization to see if IndySoft can help you manage your assets as well.
Ready to take the next step?
WE ARE, TOO.
Fill out the short contact form and we'll get in touch shortly to answer all your questions and schedule a demo.
Let's Talk